
.jpg)
“It helps analyse the process and see how the weld pool is behaving. “The magnification is terrific and we can easily identify any inclusions or flaws,” says Mr Weston. Installed in the summer of 2010, the impressive magnification of the ZIP Lite's lens is also used by MTT to examine the surface roughness of SLM produced components, as well as material density. However, using the ZIP Lite to measure the first-off means MTT can identify any problem areas, feed this information back to the CAD model and subsequently produce a perfect artefact. While the SLM process is ideal for complex, lightweight parts, the inherent nature of SLM means parts exhibiting substantial cross sections can sometimes demonstrate minor levels of distortion or shrinkage. Furthermore, multiple parts can be constructed simultaneously on the same build plate.Īnother use for the ZIP Lite at MTT is the production of artefacts. Using scanning speeds of up to 2,000mm per second and build rates of up to 20cm³ per hour, parts are produced in only a few hours. Sectors such as dental, medical/orthopaedic and aerospace are all exploiting the many benefits afforded by SLM, such as the creation of very complex geometries that would prove almost impossible using conventional subtractive machining techniques. With 90% of the company's SLM machines destined for export markets such as Germany, France, Italy and the USA, MTT says the past couple of months have seen a marked rise in demand as the global economy strengthens. Compensation is then applied in a system calibration file. The ZIP Lite measures the difference at each outside edge and the straightness of each axis, allowing MTT to introduce compensation that guarantees a centrally located build at exactly the correct size. A 250mm by 250mm build plate is used on MTT's standard SLM250 model, and each newly constructed machine is asked to create a square at the extremes of the build area. The OGP machine at MTT also allows the company to ensure its laser is square and centred perfectly on the build plate. Put very simply, without the ZIP Lite, we couldn't make machines this accurate.” This is a process we can iterate many times if required, ultimately achieving accuracy down to 0.03mm and beyond.

“From the results we can see precisely how much compensation we need to apply to each individual machine. “An important function of our ZIP Lite is to scan a standard grid produced by the SLM and to measure various points to check for variations in X-Y,” explains Mr Weston.
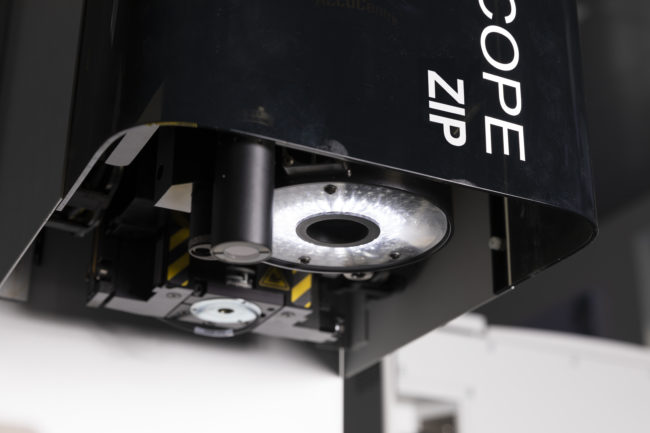
The laser has a focal distance of around 400mm to the object being manufactured, but with machine build tolerances in the region of ☑mm, a reliable method of compensation is required to guarantee accuracy for SLM machine users. The X-Y head features two highly responsive scanning mirrors capable of translation/positioning speeds of 7000mm/second, so even the smallest of errors can have a negative effect.
#SMARTSCOPE ZIP SYSTEMS SERIES#
From source, it is directed through a series of optical components before entering the X-Y scanning head, which is used to direct the laser. The laser is at the centre of the SLM machine's operation. Parts are built from a range of fine metal powders (including cobalt chrome, stainless steel, tool steel, titanium, Inconel and aluminium) which are fully melted in a controlled atmosphere, in layers as thin as 0.02mm. SLM is a pioneering, additive manufacturing process capable of producing fully dense metal parts direct from 3D CAD models using a high power fibre laser. Furthermore, because we have SLM machines installed at customers all around the world, OGP's international presence was very appealing should a field accuracy problem ever occur.” OGP also provided an impressive product demonstration and performed measurement trials. For instance, OGP were very patient and understanding, and listened carefully to our requirements, advising impartially on optimum solutions. “In our search for a suitable metrology solution we assessed a number of leading players, but several factors set OGP apart from the rest. “We realised some of our competitors had better ways of ensuring machine accuracy,” says MTT's group marketing manager, Robin Weston.
#SMARTSCOPE ZIP SYSTEMS MANUAL#
However, until recently the company used manual methods or opted to subcontract the task of calibrating the range of SLM machines it builds at its headquarters in Stone, Staffordshire. With a turnover in the region of €15-20 million generated by 80 employees at locations across the globe, MTT can count itself as a major player in SLM technology. As well as enhancing the accuracy of its SLM series rapid manufacturing machines, the ZIP Lite has also allowed MTT to eliminate the costly and protracted subcontracting of measurement/calibration tasks.
